石油炼制是现代工业的基础,提供了90%以上的交通运输燃料和化工原料,是世界上最大、最重要的加工工业之一。而炼油工业除常减压、焦化等少数几个过程外,80%以上的过程为催化反应过程,催化剂成为实现原油高效转化和清洁利用最经济、最灵活、最有潜力的关键核心技术,是炼油技术进步最活跃的领域。
中国石油年炼油能力已接近2亿吨,催化剂年使用量约7万吨。但在“十二五”之前,中国石油除了在催化裂化催化剂和硫黄回收催化剂领域具有传统优势外,其他重要的炼油催化剂研发还处在起步阶段,高水平炼油系列催化剂的开发成为制约公司炼油技术进步、加快实施国际化战略的瓶颈。
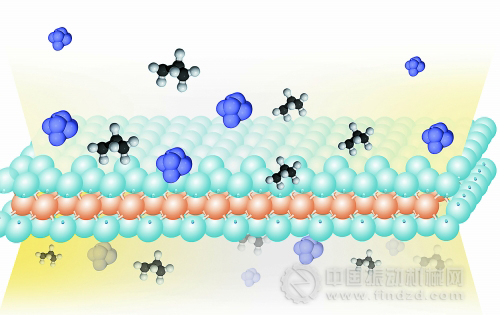
炼油催化剂作用机理示意图
快速突破催化剂核心技术,开发具有自主知识产权的炼油系列催化剂,消除瓶颈、补齐短板,建立完整的炼油技术链条,尽快形成中国石油炼油业务的新优势,全面提升中国石油的炼油技术水平,成为摆在广大科技工作者面前迫在眉睫的一项重要任务。
历史是何其相似,新中国成立之初,炼油工业处于一穷二白的起步阶段。为打破国外技术封锁,老一辈科技工作者在石油部的统一组织下,开展了自主研发催化剂的大会战。炼油催化剂成为我国炼油工业的基石,其中生产高级航空汽油的硅铝小球催化剂为我国国防建设做出了重大贡献,被称为名副其实的“争气剂”。
如今,炼油工业面临原油重质劣质化、过程环保绿色化、产品清洁高质化等严峻挑战。针对这一紧迫需求,科技管理部会同炼油与化工分公司通过顶层设计,组织大团队、集中大投入,全面布局重要炼油系列催化剂的研发,坚持自主创新、重点跨越、支撑发展、引领未来,承担行业技术创新责任的目标,于2010年适时启动实施“炼油催化剂研制开发与工业应用”重大科技专项。专项由石油化工研究院牵头,兰州石化、抚顺石化、西南油气田和中国石油大学等26家单位近700名科技人员进行为期4年的协同创新,重点攻关。
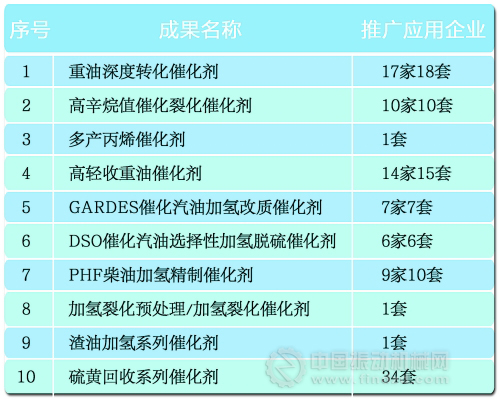
中国石油自主研发主要炼油催化剂工业应用情况
“十二五”期间,通过重大科技专项的实施,以催化裂化催化剂成功拓展海外市场、汽柴油加氢系列催化剂全面支撑油品质量升级等为代表,自主创新的技术从无到有,从少到多,中国石油在炼油催化剂关键领域取得了重大突破,同时带动催化新材料、催化反应过程和催化剂生产技术的全面提升,取得了丰硕成果。广大科技人员团结拼搏、攻坚克难,向集团公司党组交出了一份圆满的答卷:攻克了56项关键技术,研制开发了六大类、21个系列52个品种的催化剂新产品和8个品种的催化新材料,开发出5个工艺包,申请专利154件,认定技术秘密67项,催化剂累计生产销售超过9万吨,在54家企业的111套工业装置上实现应用,新增效益20亿元以上,整体技术达到国际先进,先后荣获国家科技进步奖二等奖2项,集团公司一等奖4项。
催化裂化催化剂研发继续保持优势,开发出重油深度转化、提高汽油辛烷值、多产丙烯等四大系列17个牌号的新型催化剂,在国内外50余套装置工业应用,并成功进军海外高端市场。硫黄回收系列催化剂在国内外34套工业装置得到应用,为装置达标排放和节能减排做出新贡献。汽柴油加氢催化剂在20余套汽柴油加氢装置成功应用,成为中国石油汽柴油质量升级的主体技术。
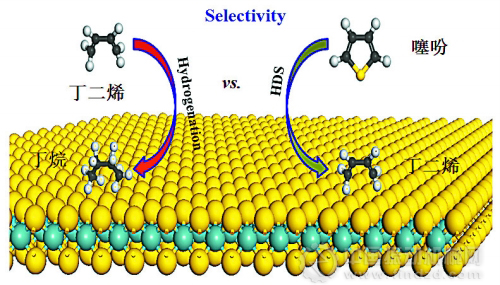
催化剂与炼油分子“亲密接触”
加氢裂化和固定床渣油加氢催化剂研发取得突破,成功实现工业应用,填补了中国石油在该领域的空白。开发的高性能NaY分子筛、低成本合成β分子筛等催化新材料成为高性能催化剂开发的基础。催化裂化及加氢催化剂生产成套技术攻关取得成功,集成开发出5万吨/年催化裂化催化剂、5000吨/年渣油加氢催化剂和1000吨/年非负载加氢催化剂生产技术工艺包,为公司炼油催化剂业务发展和生产基地建设提供了技术支持。
通过持续攻关,提高了石油化工研究院炼油催化剂创新基地和兰州、抚顺两个催化剂生产基地的研发生产水平,催化、重质油加工、清洁燃料生产三个重点实验室和催化裂化催化剂与工艺、加氢催化剂与工艺两个中试基地的研发能力和装备水平实现了质的飞跃,自主创新能力得到大幅度提高。专项攻关培养和凝聚了一支技术精、作风硬、服务优、勇于奉献的创新团队,他们已经成长为中国石油炼油技术进步的排头兵和主力军,是公司发展的宝贵财富。
进入“十三五”,面临低油价成为新常态的挑战,炼油催化剂的研发在满足更高标准油品质量升级、炼油产品结构调整、提升重油加工水平、做大做强做优公司催化剂产业需求方面,将重点开展基于“分子炼油”理念的催化剂结构设计、纳米化功能化新材料开发、高效低耗催化剂清洁生产技术等研究工作,使炼油催化剂开发实现技术模型化、平台化、成套化,满足集团公司炼化技术发展需求,推动中国石油炼油催化剂业务总体水平比肩国际一流,具备全面参与国际竞争的实力。
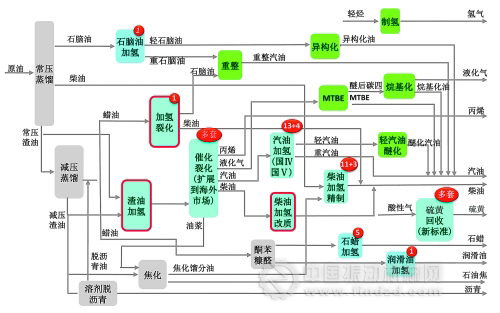
中国石油通过炼油催化剂重大专项新增3个过程(蓝底红框)的催化剂,原有4个过程(蓝底)的催化剂水平大幅提升,自主研发占全部催化过程的63%。
亮点技术
1 汽柴油加氢系列催化剂
石油化工研究院和中国石油大学联合开发了催化汽油预加氢催化剂、选择性加氢脱硫催化剂等9个牌号汽油加氢系列催化剂,形成了DSO和GARDES汽油加氢成套技术,实现了汽油深度脱硫、降烯烃和保持辛烷值,已在公司的13套装置应用,占同类装置的54.4%,支撑了中国石油汽油质量升级。PHF和FDS系列柴油加氢精制催化剂在10家炼厂13套装置成功应用,为公司柴油质量升级提供重要支撑。“满足国家第四阶段汽车排放标准的清洁汽油生产成套技术开发与应用”荣获2015年国家科技进步二等奖。
2 渣油加氢催化剂
重大专项项目组成功开发了孔结构灵活调控、活性金属非均匀分布等6项关键技术,攻克了适合渣油大分子扩散的特种大孔道载体制备难关,设计并研制出分别具有梯度孔、双峰孔、通畅孔、集中孔特色的4大类12个牌号固定床渣油加氢催化剂;实现了多种催化剂功能的优化级配,最大化发挥了催化剂脱硫、脱残炭等功效,已在大连西太平洋石化公司渣油加氢装置上成功完成工业应用试验,保障了装置的长周期、安全、平稳运行,总体达到国际先进水平,填补了中国石油在渣油加氢催化剂领域的空白。
3 硫黄回收催化剂
硫黄回收是将硫化氢等有毒气体转化为单质硫,实现变废为宝保护环境,是炼油、化工和天然气净化过程的重要环节。
西南油气田公司研发出了4种类型9个牌号的系列硫黄回收催化剂,开发形成了常规及低温克劳斯、有机硫水解、硫化氢选择性氧化、克劳斯尾气加氢水解等技术,整体水平国内领先,优势领域达到国际领先水平,已在重庆天然气净化总厂、独山子石化公司、广西石化公司等企业的34套装置实现应用,国内市场占有率达到75%。
4 加氢裂化催化剂
加氢裂化技术是唯一能在重油轻质化的同时直接生产车用清洁燃料和优质化工原料的工艺技术。
石化院开发出了活性稳定性好、中间馏分油选择性高、异构性能强的PHC-03加氢裂化催化剂,在大庆石化120万吨/年加氢裂化装置成功实现工业应用,液体产品收率达到99.37%,与柴油和航空喷气燃料收率相比提高3%,柴油凝点低5摄氏度,尾油BMCI值低2个单位。该催化剂的成功开发及应用填补了中国石油自主加氢裂化技术领域空白。
5催化裂化催化剂
石化院在国际上提出了正碳离子“晶内产生、晶外传递、表面裂解”的重油催化机理新观点,成为高水平催化剂设计的理论基础;以自主研发的Y型分子筛结构二次修饰技术、ZSM-5活性恢复、重金属涂层捕集等关键技术为核心,显著提高了催化剂抗金属能力,开发出了重油高效转化、提高汽油辛烷值、多产丙烯等系列催化剂,在国内外50余套装置得到广泛应用,并成功进入北美高端市场,产生经济效益12亿元以上,使中国石油自主技术生产的产品比例提高到92%,国际竞争力进一步增强。
6 催化新材料
为进一步提高NaY沸石工业生产技术中产品结晶度和硅铝比,中国石油依靠自主研发的多项专利和专有技术,针对高硅NaY分子筛性质特点,通过营造“晶核形成”和“晶体生长”两种不同化学环境的技术方法,开发出具有晶化时间短、结晶度高和较高硅铝比的高性能NaY沸石合成成套技术,满足了生产高性能催化材料的生产急需,以此为原料生产的分子筛活性组分在LDO-75、LDO-70等19种工业催化剂中获得大面积成功应用。此类材料的成功开发为今后研发系列新型催化剂奠定了材料基础。